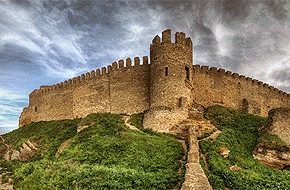
By Bernard Hickey
A Fonterra-board appointed inquiry into a recent Botulism scare has recommended Fonterra change its plant cleaning procedures, employ more communications people and shed a reputation it has with its clients and regulators for being "Fortress Fonterra."
The Inquiry led by Chapman Tripp partner Jack Hodder, QC, made 33 recommendations to the board after looking into the events leading up to and after Fonterra recalled a batch of Whey Powder from infant formula manufacturing clients and others because of initial test results from AgResearch appeared to show signs of a bacteria that can cause botulims. One of those clients, Danone, has since claimed damages worth more than 200 million euros from Fonterra.
The report found a lack of senior oversight of crucial decisions, problems with tracing potentially affected product and belated escalation of the issue contributed to the "event" in August this year.
The full report detailed (pages 37-56) the timeline going from February 2, 2012 when a plastic torch was broken in a Hautapu vat to the August 3 announcement that tonnes of whey powder could be contaminated with botulism. Eventually, it was proved not to be contaminated.
“There were shortcomings in a number of areas, which, compounded by a number of events and co- incidences, converged to create this significant issue," Hodder said, adding the inquiry had not found any fundamental problems within Fonterra, noting however a range of improvements could be made.
The board had agreed to reconvene the Independent Inquiry Committee in nine months and again in 18 months to review the progress against the recommendations.
"The Board should actively review ongoing progress towards shedding the adverse “Fortress Fonterra” perception held by a material proportion of external stakeholders," the report said, adding that Fonterra board members needed to take more responsibility for improving relations with Government and the media.
The Inquiry found:
1 Fonterra did not include any sulphite reducing clostridia (SRC) tests to any of its production of WPC, notwithstanding its acceptance of SRC tests under at least one contract with a major customer to manufacture products utilising WPC80.
2 Some errors of judgment were made in preparation for the reworking process applied to the relevant WPC80 batches.
3 The standard pre-start up automatic cleaning regimes used by Fonterra plants required improvement. 
4 There was insufficient senior oversight of the crucial decision to engage AgResearch to test for C. botulinum.
5 The commissioning, design and limits of the C. botulinum testing were inadequate.
6 Fonterra was unable to promptly and definitively track the destinations of the affected WPC80 batches.
7 There was only belated recognition (and delayed escalation to senior management and the Board) of the explosive reputational risk involved – a failure to “join the dots” between (a) C.botulinum (b) infant food products (c) consumer sensitivities and (d) Fonterra’s global reputation.
8 Fonterra’s crisis management planning, including the external communications aspects, was inadequate for an event of this kind and scale.
9 Fonterra management of the events in the critical early period, including the external communications aspects, was not well executed.
10 There was some lack of alignment and confidence between Fonterra and the New Zealand Government in the critical fortnight after the contamination concerns were advised to the Government and made public.
The Inquiry recommended the following to Fonterra:
1. Fonterra’s food quality and safety specifications and testing be reviewed to ensure they are “best in class” standard: consistent with the most rigorous requirements of customers, and with international best practice.
2. Risk management and crisis management processes be strengthened, including by establishment of a specially trained and multi-disciplinary (but not full-time) Incident Management Team and regular relevant training, global best practice product tracing systems, and a new Risk Committee of the Board.
3. Reputational risk assessment form part of the criteria for escalation and assessment of non- standard external scientific tests.
4. Plant cleaning programmes be amended.
5. There be continued building of a directly-employed strong, specialist and experienced communications team, including in key global markets, supplemented with contracted high calibre local expertise where appropriate.
6. There be enhanced and sustained efforts to address a “Fortress Fonterra” perception held by a material proportion of key stakeholders, by Fonterra redefining the style and substance of its engagement with them.
7. The Inquiry be reconvened after 9 months and again after 18 months to review Fonterra’s progress on those recommendations.
It recommended to the board:
1. The Board should endorse explicitly as a core principle that Fonterra, as “one company”, always strives to perform at the best practice level for leading global food product organisations.
2. The Board should explicitly endorse the paramount importance of food quality and safety to Fonterra’s global and local reputation.
3. The “risk” component of the Board’s Audit, Finance and Risk Committee should be transferred to, and developed by, a new Risk Committee.
4. The Board should accept greater responsibility for developing and maintaining relationships at the most senior levels of Fonterra’s external stakeholders, including in government and media, within and outside New Zealand.
5. The Board should actively review ongoing progress towards shedding the adverse “Fortress Fonterra” perception held by a material proportion of external stakeholders.
Political reaction
Prime Minister John Key said later he welcomed the report and had "complete confidence in Fonterra". He downplayed the comments about 'Fortress Fonterra'.
Later, Labour Leader David Cunliffe that Fonterra had to "up it's game."
“The inquiry released today shows that Fonterra is a silo-driven company with too much emphasis on production, has patchy regulatory interaction and a fortress mentality," Cunliffe said.
“The report shows Fonterra has some way to go before it can be regarded as a uniformly world-class producer of high-value food. It criticises the focus on production volume rather than the need to maintain uniformly top class quality control. When exporting high quality product for human consumption there is no room for a number eight wire approach. Fonterra has to get it right every time and have 100 per cent quality and safety standards," he said.
7 Comments
I have another suggestion for them. Find another use for milk powder than infant formula, as the Chinese govt have decided to actively promote breast feeding for infants and are legislating for what sounds like almost plain packaging on containers and that they must also have on them information promoting breast feeding.
This news comes after the botulism scare, but it also comes very hot on the heels of all the news of US spying on mates and presumably, not mates, and the possibility that we have been part of it (what other conclusion could you draw from what John Key said) and us back playing cowboys and indians with US.
I also thought Chinese mums should be breast feeding, but we have built up a huge industry on them not, and could be looking at it being seriously dented
As the Commerce Commission warned when Fonterrible was formed , if the NZ dairy industry is operating predominately under one banner , the risk of a screw-up impacts upon the entire industry .... and indeed , the entire country ...
... had there been greater competition , and less of the too-big-too-fail hubris , other processors would've taken a chunk of Fonterra's supply by now ....
But in reality , it's business as usual down at the hulking dairy behemoth ...
If processors paid more for the milk they would be able to secure supply, simple as that. Since dairy board was deregulated by the government, and then reregulated (DIRA) by the commerce commision, I don't know what advances have been made. I suppose NZ suppliers aren't as bad off as those in Australia (according to David Chaston).
Apart from the biological impossibility for the C.Botulinum to grow in the first place, in a normal dairy factory environment, there is an issue with staff and people employed by Fonterra, which was initiated by senior management as the industry became more profitable and so had more money to pay the higher salaries of University Graduates.
Fonterra started employing University Graduates about 10 years ago, with degrees in various subjects, some relevant some not. Fonterra also put in place an internal Graduate Training Program. As an Industry they had not been exposed to before they would find it a new challenge, but they wanted a meaningful job.Some of these people stayed, some left. Some were put into management positions.
The point is that, many of these graduates, do not have specific training in Dairy Products or Manufacturing Technology. This training is available from Massey University, and they have trained many of the previous Factory Managers that have served the Industry extremely well for the previous 50 or 60 years. The Dairy Manufacturing Operations of today are more complex with Computers/PLC's and scale of size, etc, but the basics of good Dairy Product Manufacture remain.The people put into those courses had to have worked within the industry for several years before going to Massey, and were selected by the individual Dairy Company mangement on suitablity and performance.
A Message to " Gummy Bear Hero "
Before Fonterra was born-- it was operated under one banner, through out the world, it was called " The NZ Dairy Board " and if this problem had occured then it would have been at an individual Company and an Individual Manufacturing Site, just like now.
If the hit had to be taken by one of the individual companies, that comprised the former NZ Dairy Board -- then that company may have had to take the financial hit, and because of their small size would go bankrupt.
In this case, since Fonterra has more coin, the whole industry will share the hit !!!
But hopefullly Fonterra has Insurance cover for this type of event because it
is a huge risk of the business. That is the Dollar Loss.
What is more critical is the Loss of Trust of manufactured product quality,
which is very hard to quantify !!! and will take years to repair.
By Jingo's Jack, a lovely point you make but we're not allowed to shout at each other, and trust me GBH would have read it, he's a reasonable sort like that.
So er , you know, um, just keep an eye out for Gareth with the shouting thingy there , he takes a dime view of that sort of interaction.
Should've gone to Specsavers...eh.
Yasssss , ole Gummy can remember the NZ Dairy board .. .. kinda hoped we could get more competition into the industry ... .. but Herr Helen overuled everybody ... and we got Fonterrible ....
... he does shout a tadge , our Jack !
Ewe're right as usual , good Count ...
We welcome your comments below. If you are not already registered, please register to comment.
Remember we welcome robust, respectful and insightful debate. We don't welcome abusive or defamatory comments and will de-register those repeatedly making such comments. Our current comment policy is here.