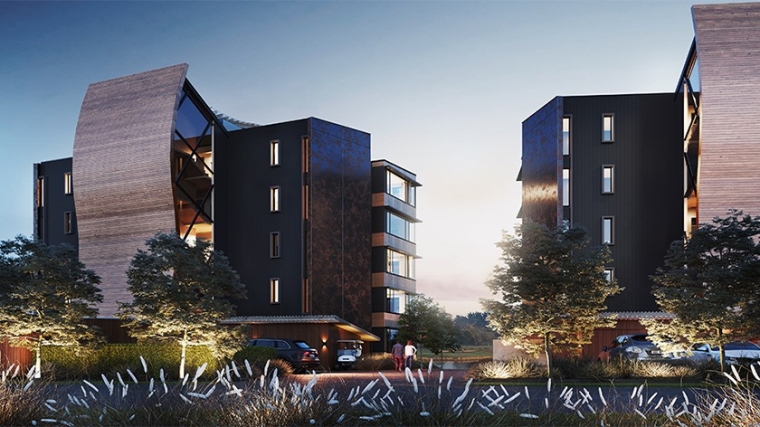
By Brendon Harre*
An abridged report.
The planet is on fire. Humanity is responding - hopefully fast enough.
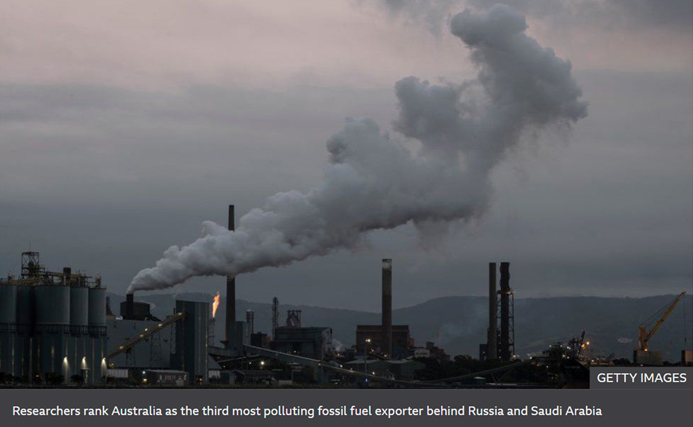
Source BBC News article — Australia attacks sweeping EU climate plan to tax imports
Europe’s coal and steel union evolved into the European Union. Which is now evolving into an environmental union that intends to tax imported carbon. Such a tax would make exporters to the EU pay more for goods like steel and cement.
The global warming threat to humanity and the international response has significant implications for New Zealand. The country should carefully consider its position.
Australia is attacking the EU plan, but if the US follows the EU lead, then Australia will eventually follow too.
It is not in New Zealand’s best interest to align with Australia’s slow game plan.
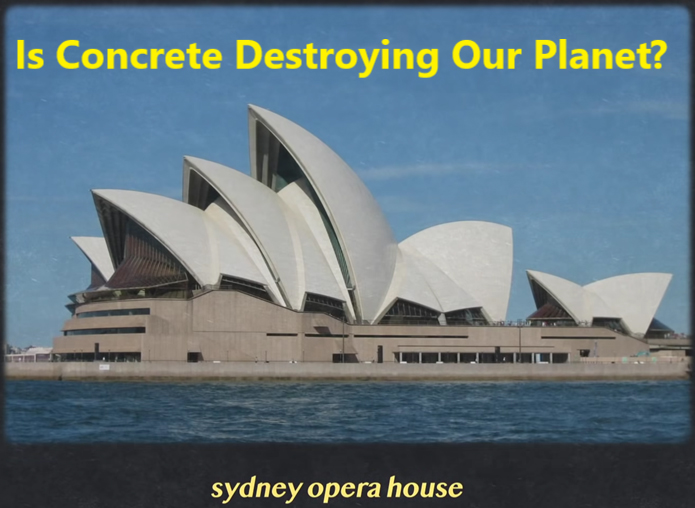
Cement and steel in reinforced concrete is one of the least mentioned contributors to greenhouse gas emissions. Source — YouTube video — Is Concrete Destroying Our Planet?
A fast climate change agenda has economic opportunities for New Zealand — an open-minded view of the situation would see the opportunity. In particular, that New Zealand can take a globally important role in reducing construction related CO2 emissions.
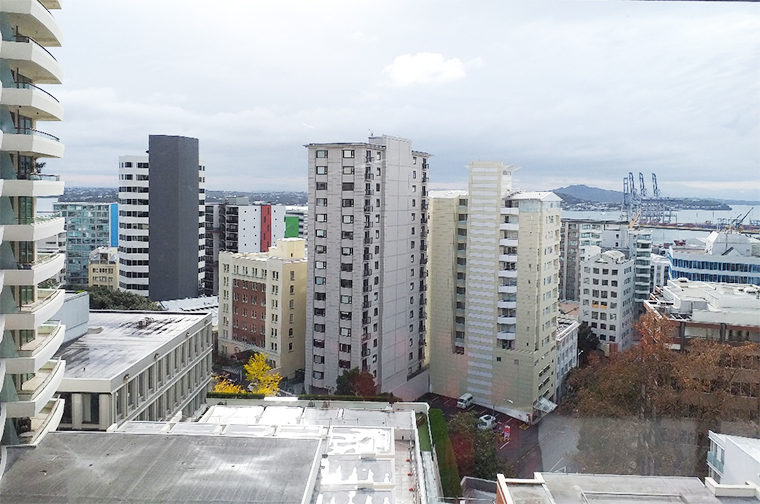
Photo taken by author from Auckland’s Pullman Hotel MIQ. Constructing this built environment must have emitted thousands if not millions of tonnes of CO2. Yet it represents one of the solutions to the climate emergency. It is a genuine walkable environment where the requirements of life — employment, residential, retail, entertainment, education, healthcare, and so on — are in close proximity.
For a century-and-a-half large buildings in the world’s cities have been constructed from steel and concrete.
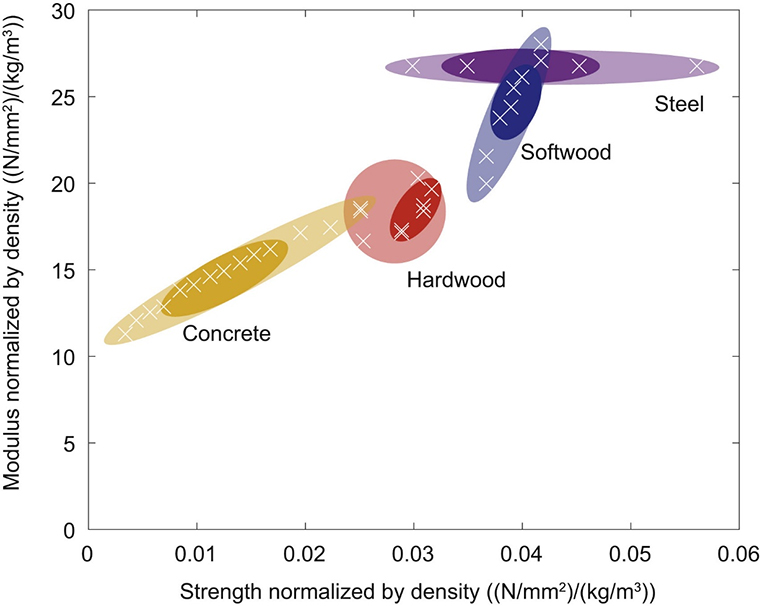
Fig. 21. Compression strength and modulus of construction materials normalised by density, according to the relevant design standards — the dark colors represent the more widely used grades of material. Design values of strength and stiffness, including partial factors, are shown, based on the Eurocode design standards for concrete, steel and timber. Source
There is now an alternative — wood has the structural properties to be an engineered building product.
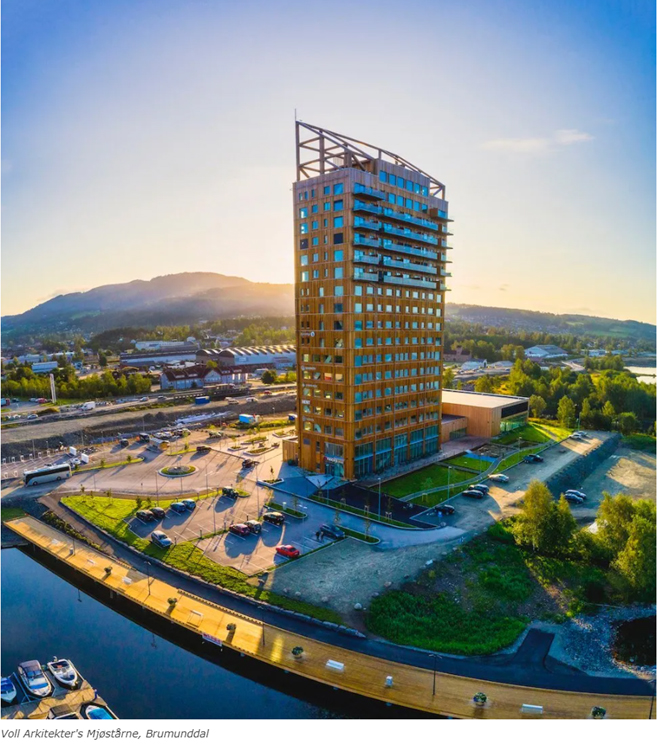
Source — Top 5 tallest timber buildings in the world article
As a result of timber research, on issues like fire protection, restrictions on building larger buildings from wood have been relaxed.
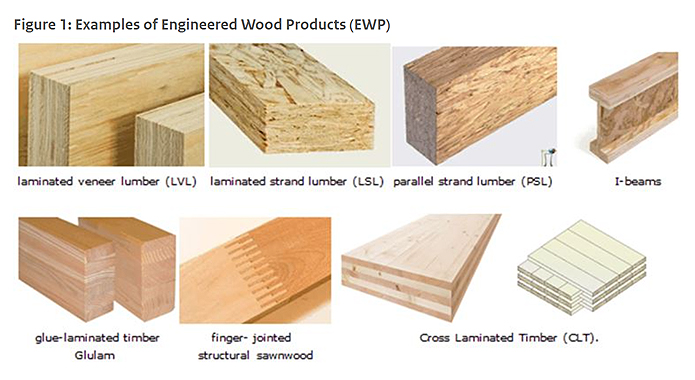
Engineered wood products are becoming increasingly sophisticated.
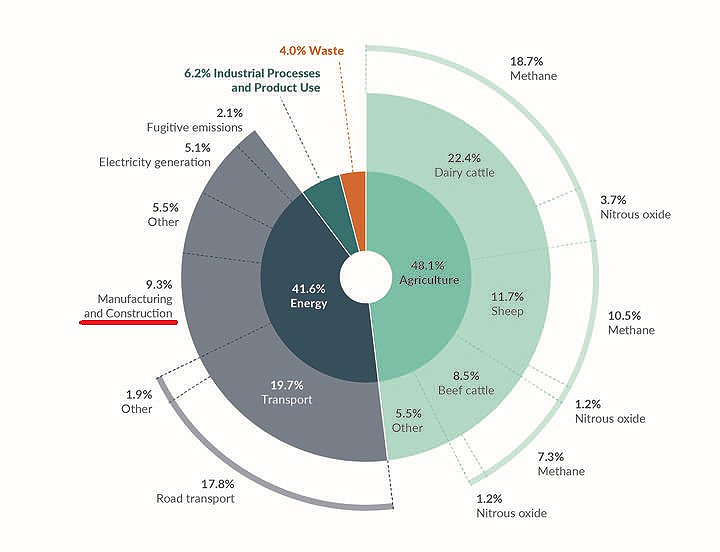
Gross greenhouse emissions for New Zealand in 2019. Construction emissions are smaller than some other emitters, such as, transport but it is significant. Note gross emissions refers to total emissions. Net emissions are gross emissions minus emission removals from land use, land use change, and forestry. Source.
Concrete and steel together account for 14.7% of global carbon dioxide emissions. Construction and manufacturing are 9.3% of New Zealand’s gross emissions.
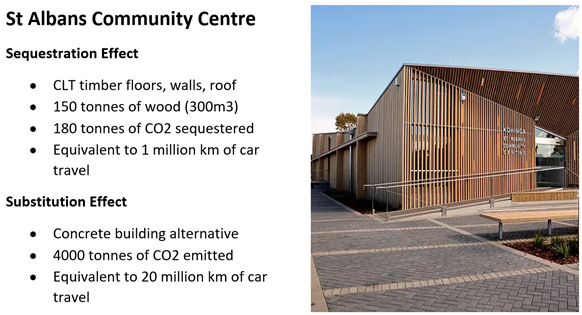
Carbon stored (sequestered) in Christchurch’s engineered wood constructed St Albans Community Centre building compared to concrete and steel construction. Figures provided by Prof Buchanan in a talk about timber buildings and carbon forestry
The proposal is simple — for climate change reasons cities need a new diet. Less concrete and steel — and more plant-based construction materials that sequester carbon, such as, engineered wood. This could be called the vegetarian city model.
Currently, the majority of New Zealand’s wood exports go to China as raw logs. Last year 80 per cent of the country’s $2.8b log trade was earned in China. There are concerns that New Zealand is overly reliant on this one market.
There are also concerns about the methyl bromide gas used to fumigate logs for export.
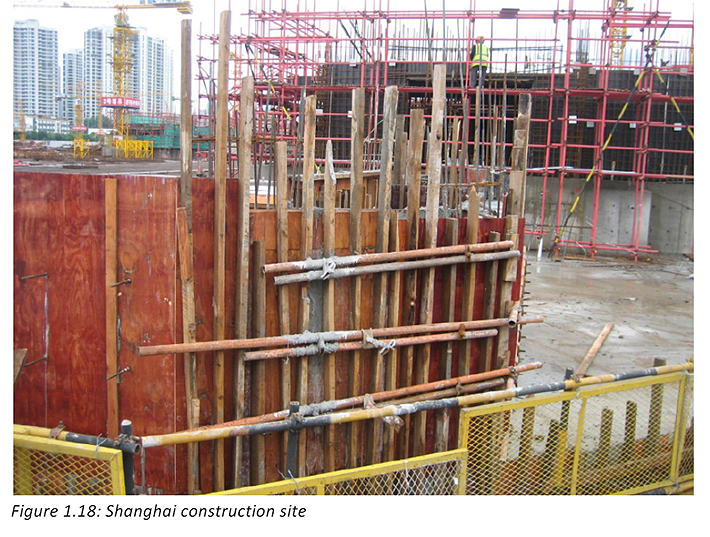
About half of NZ log exports to China becomes solid lumber or plywood used for concrete formwork. Source — Material flow and end-uses of harvested wood products produced from New Zealand log exports. Technical Report. August 2016
A 2016 technical report showed that from New Zealand’s 10.38 million cubic metres of log exports to China – 2.48m m3 was processed into solid lumber and 2.36m m3 into plywood, both of which were used for temporary purposes as form-work for concrete construction. Because of these factors the timber exports were estimated to have an average half-life of only 6.6 years.
New Zealand produces tens of millions of cubic metres of sustainably managed wood each year, much of which is exported. Currently there is a global shortage of wood products which is further discussed in the extended version of this report.
New Zealand should aim for its pipeline of timber exports to go into long life-cycle products that sequesters carbon for decades — centuries even — not years.
What technologies can help cities go on a plant-based diet?
Accoya — British company Accsys Technology manufactures Accoya using an ‘acetylation’ process in a Netherlands factory that turns fast-growing, sustainably-managed softwood into Accoya – a wood that has the durability and dimensional stability properties of slow-growing, tropical hardwoods without the accompanying deforestation and habitat loss.
The proprietary acetylation process removes water-loving hydroxyl compounds and replaces them with naturally occurring acetyl groups. This means Accoya has barely any swelling, warping, or cracking, and a much slower decay rate. Accoya offers an unrivalled 50-year warranty for wood durability. Accoya is non-toxic and 100% biodegradable.
Pinus radiata is recognised as the wood most suited to the Accoya process. In New Zealand pruned logs are processed into dried clear boards that are then exported to the Netherland factory for the acetylation treatment and some Accoya is re-imported back into New Zealand. The value-added process according to Farmers Weekly is as follows. The pruned log is sold by the forest owner for about $180 m3, the clear board processing in New Zealand raises its value to about $1000 m3, and the Accoya that is re-imported back to New Zealand sells for about $3500 to $4000 m3.
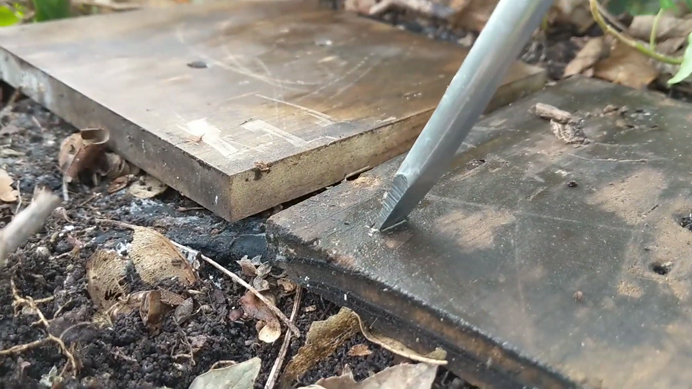
A seven-year field experiment where Accoya nailed to a stump is compared to a typical softwood
Accoya is used to make windows and doors in the UK. A joinery manufacturer explains why Accoya is such a good option for his industry in this video (the field experiment is very revealing).
Wood City Helsinki — the harbourside city block where the buildings are constructed with engineered wood. These buildings are clad in Accoya.
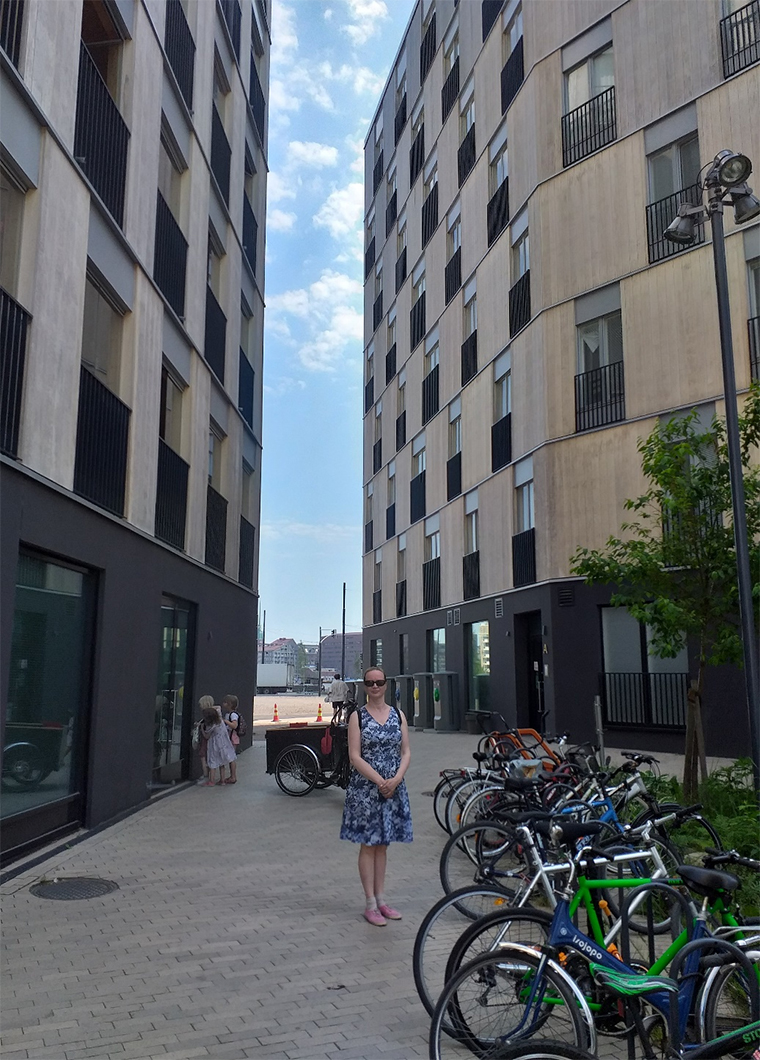
Cladding in Finland.
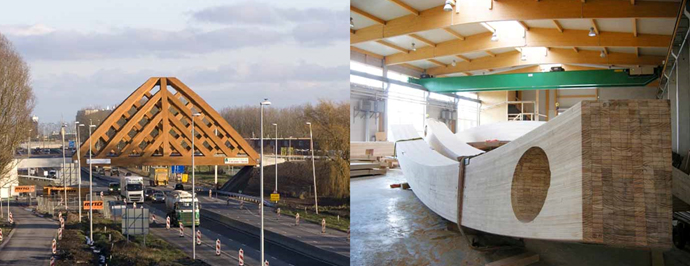
Achterbosch Sneek bridge and one of its arches. Source
A motorway bridge and canal walls in the Netherlands.
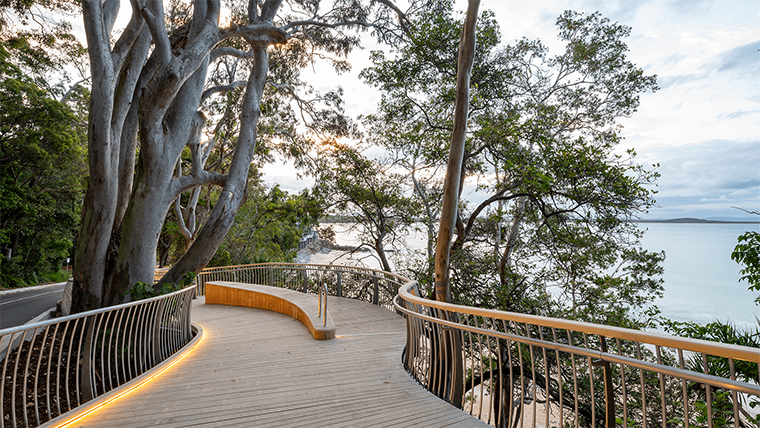
400m long boardwalk — Sunshine Coast
Decking in Australia.
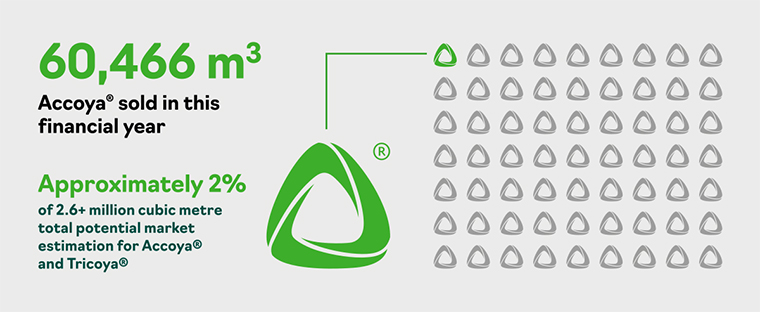
Source — Accsys-Our Markets viewed 6.7.2021.
Going forward, both Accsys and the New Zealand wood industry want to expand and diversify its markets — Accsys believes it is currently only catering for 2% of its potential market.
Optimised Engineered Lumber (OEL) – is a commercial product developed in New Zealand. It is structural lumber beams constructed from the stronger and weaker parts of a tree trunk in a way that optimises the amount of wood recovered from each log and the strength of the resulting wood products.
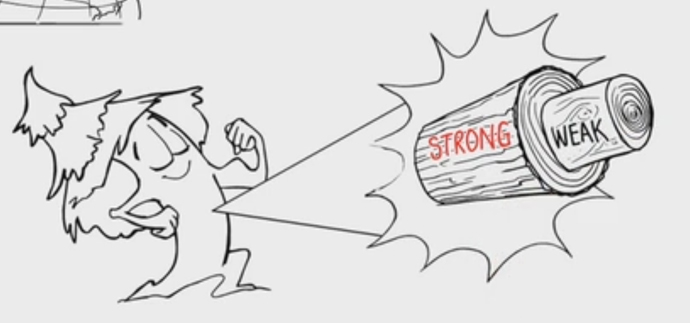
OEL learns from trees — one of nature’s strongest organisms — how to combine the strong and weak parts of the tree trunk. Source
OEL is made from thin strips of wood that are finger-jointed and laminated together. By laminating the wood, the stiffness and strength is improved. The OEL process means the whole log can be used to make high quality structural products, whereas previously much of the log could only be used for low value uses.
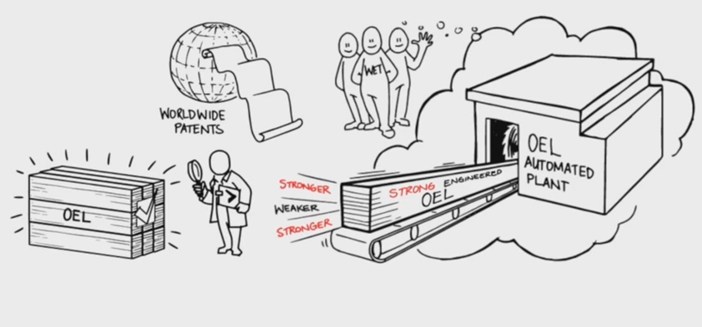
The first OEL plant was opened in Gisborne by Wood Engineering Technologies (WET) in June. When fully completed it will have six production lines producing up to 140,000 cubic metres of OEL — enough for more than 11,000 houses — and employing more than 130 people.
Cross laminated timber (CLT) — Red Stag Timber, an independent and privately owned timber company based in Rotorua, will shortly open a new $50 million wood processing plant. The Red Stag facility will have the capability to produce CLT panels that exceed 16 metres by 4 metres in size. This will allow for fewer connectors and an overall faster construction process.
The plant will add 5% to the capacity of the New Zealand wood processing sector. That equates to around two thousand dwelling units.
Red Stag group CEO, Marty Verry, said
“CLT has a value sweet spot in large-format structures, buildings of three stories or more, and for mid-floors in terraced housing built to the NZS 3604 standard. Apartment buildings and fast-to-install CLT mid-floors will be our residential focus areas.”
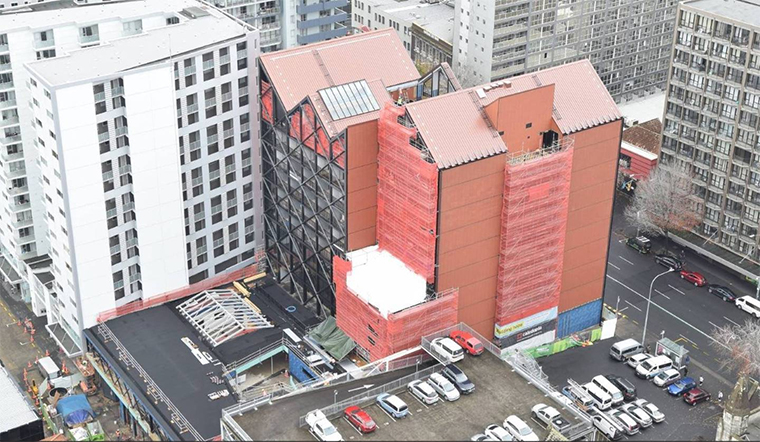
HomeGround building : the new $110m Auckland City Mission HQ is being constructed from CLT
Substituting for wood in the built environment has already begun to change New Zealand cities. There is plenty of potential for more change. The better New Zealand becomes at constructing its own built environment in engineered wood, the better it will be at exporting these high value wood products overseas for the planets benefit.
Further reading:
Engineered-wood can be used in the construction of bridges (link and link).
There are many technical papers describing the timber construction opportunity.
Financial investors have identified modified Pinus radiata as an investment opportunity.
Engineered timber is cost competitive with steel and concrete.
A farm forester describes the Accoya wood industry opportunity for New Zealand.
What if wood could be welded like steel?
What if carbon fibre reinforced wood could replace steel reinforce concrete?
This is a repost of an article here. It is here with permission.
43 Comments
Sounds nice but does NZ have the scale and know-how for this to work beyond anything beyond a niche segment of the market?
If NZ-Inc doesn't develope engineered-wood at scale then it will be a missed opportunity - IMO.
... another fantastic article , Brendon : good on ya ... awesome !
Thanks for the kind words Gummy
Considering all wood manufacturing and engineering plants have been cut and shutdown over the last decade because processing, manufacturing with renewable energy in NZ is seen as causing climate change by the zeitgeist compared to shipping with fossil fuels to coal powered factories overseas and then shipping back there is very little hope then. Even the example OEL plant has been hit and restricted. Most skilled wood engineers have left, the sector is drained, most processing and manufacturing businesses have closed up in NZ. The work for large scale processing is not in NZ and much fewer jobs are available than for even dominos franchises. The green protests and govt achievements have increased our reliance on overseas coal powered wood processing and massive waste dumping & rainforest stripping. Come back next generation when they finally realize NIMBY climate initiatives do more harm as they do more to increase coal burning and waste energy through logistics and crash many productive sectors that could lead the way on global environmental scale for base needs. Until we return processing and manufacturing back into NZ at large available scale there will be no great movement of change towards a far less affordable and less resilient (both in supply and lifetime use), material for what is needed on large scale construction. Even the national award leading wood architects and their pet engineer could not think through how to manage construction on a low height convention center without massive disaster. Tall multi use skyscrapers are out of their skill set.
... the Accoya technology was originally developed in Rotorua by Scion ....
In 2008 the Netherlands had a 30 metre long , 12 metre wide bridge constructed from Accoya timber .... its rated to withstand 60 tonnes of load ....
Yeah I wrote about the Scion angle in the extended version of the report. I think the bridge you are referring to is the motorway overbridge I show.
"wood" be interesting to hear about that? How did accsys get the patent granted if there was prior art? Did scion sell or license the IP? Or did accsys come up with a novel fancy method for drying the wood, dipping into acetic anhydride and heating to 120 degrees?
Scion sold IP developed from experimenting with a small scale acetylation pilot plant to Accsys in 2006 is my understanding. Accsys developed the process to a commercial scale so have added considerable IP. Also Accsys has spent 15 years building a brand around Accoya - making the sustainability regulatory argument in particular.
Thanks. It seems a bit depressing to forfeit the value from the IP, but I guess that’s hindsight. Maybe this paves the way for other types of chemically modified wood to be commercialised. Maybe urethanes instead of esters could be the next thing.
Thanks for this, Brendan. A question: do we have data on the embodied energy in engineered timber cf. with steel & concrete? That is, there's obviously quote a bit of energy involved in felling, transporting, milling, engineering, re-transporting to market, then to site etc. With all of that, I presume it's still ahead of steel & concrete for energy use?
Not embodied energy but the CO2 emission figures from Prof Buchanen included the whole production chain including felling and transport.
It will be much less though.
Pruned radiata pine is the ideal choice for the Accoya process, so it looks like we will have to start pruning again. I wonder if Accoya is a patented process and if so what would be involved to set up production in NZ?
Radiata clears are a unique resource. But can it pay a premim high enough to make up for lost stand volume.
Yes profile that is something I often think about. I will probably start to prune some of our recent plantings to hedge our bets. Don't know whether I will be around to see the harvest but at least it will give options for the future.
There is simply no comparison in CO2 emissions. Concrete and steel are way worse, even after accounting for the little known fact that concrete reabsorbs about a third of that CO2 as it ages over the centuries.
Yet ironically in NZ we have pine forests being locked up in tax payer funded carbon schemes and pricing out lumber.
You are only talking a fraction of our forest estate in permanent forests. There is in fact incentive to plant production forests using carbon in the first rotation which will benefit our future wood supply.
I'm seeing production forest being locked up not permanent carbon forest. Even pruned blocks. Jobs, export earning and domestic lumber lost to taxpayer funded virtue signalling.
Conc slab floors absorb heat and radiate slowly throughout the night without extra heating making cost effective and efficient home heating. Super-home movement have stats to prove it
I can see how that would work with direct sunlight hitting the slab, but if it's just under the house how much heat would it really absorb? And does that offset the carbon used in its production? Also, what happens about the plumbing with a concrete slab?
I heard that there is underfloor heating connected to a heatpump. With a minimum operating the heating the slab warms and the heating is turned off overnight. Maintains 18 deg even when it is a frost outside. There are stats to prove it which you can check, rather than just big claims by a sales rep
I can see how that would work with direct sunlight hitting the slab, but if it's just under the house how much heat would it really absorb? And does that offset the carbon used in its production? Also, what happens about the plumbing with a concrete slab?
Also, what about concrete sweating? https://gambrick.com/why-does-concrete-sweat/
Solar thermal mass pays it's way in carbon terms. The pour is once, the gain is every day forever. Yes, the sun needs to get to it (unless you use water, cleverly) but the problem is that we have to set ourselves up (using the remaining FF; there's nothing else) for a post-FF era. Few get their heads around this - the usual dodge is to concentrate on Climate, while assuming growth in everything else. It won't be like that. What we need is as resilient a housing-stock as we can manage, before we have no room to move (energy-wise).
Hang on, many of the examples are on the display cladding side which is not what you are addressing. You want to show primarily only structural end construction. Even weak plaster can be used for cladding and wood cladding or outdoor pathways is not new (existed and used for millennia). It is just unfashionable to high paid office bureaucrats for government buildings when compared to expensive stone and glass monuments.
I gave one accoya cladding example.
I also gave the following examples
-Accoya decking
-Accoya external window and doors
-a bridge made from Accoya glulam beams
-buildings made from pinus radiata CLT walls and glulam beams.
Pacifica if you want to believe wood has no future in NZ then that is your prerogative. In my opinion I have presented enough evidence that most people will believe otherwise.
Accoya decking
Accoya external window and doors etc we have had for ages. There are buildings in NZ with the original wooden doors from over 100 years ago. "Pacifica if you want to believe wood has no future in NZ" if you are too arrogant to read my comment then don't bother to make up a argument to attack. I never said anything close to wood has no future and it would be highly ignorant for you to assume such as I have sustainable engineering experience with composite wood products (albeit on the smaller residential and commercial business end).
Oh wait I just realized you think the doors, window frames and exterior coverings are structural elements holding up the building weight and are somehow newsworthy if they are made with wood. Slow clap. Don't worry it is not a mistake made by many. Anyone who knows even back in medieval times knows wood was used for all of those things, including the latter named boardwalks. Composite wood products have been around and used in buildings for decades. Quite often in laminated forms. We had the manufacturing technology generations ago but manufacturing fell out of favor here and guess what happened to the NZ building sector over that time. Nowadays materials used are a consultant business decision and very rarely a decision available to most new builds. Even tendering processes are very rarely open, ethical and honest.
Pacifica you reach some strange conclusions.
Wood can be a great structural product. However one of the drawbacks is that it’s strength to sectional area is quite low. I.e structural timber takes up a lot of space.
Despite its high stength to density ratio it’s density is very low (<10kN/m3 vs 24 kN/m3 for concrete and 72 kN/m3 for steel). The low strength/ area has obvious drawbacks when you are trying to maximise floor area/ ceiling height.
What if strength was improved by adding carbon fibre to the glulam beams and CLT walls?
https://www.sciencedirect.com/science/article/abs/pii/S1359836818316391
Japan is experimenting with a building constructed from carbon fibre reinforced timber beams.
https://www.teijin.com/news/2018/ebd180925_01.html
Very interesting article. I recall Bob Jones voicing support for timber framed commercial buildings a while back?
Some misconceptions here.
Firstly, cities aren't a sustainable construct. Walkable yes, but that a humancentric concept. In real terms, cities are giant heat-engines, as Girarget makes clear. So the overarching question of cities is whether they're capable of being fed/energised/resourced, post-fossil energy?
Secondly, the assumption is more growth (more build). Actually, we need to reduce population, and as we do so we can triage the worst of our existing housing. A good target, within a generation (and houses outlast a generation) would be 2 million in NZ - which gives scope to triage the worst, out.
Thirdly, from an energy POV, passive-solar housing is the only game in town - again, post-FF. And passive solar needs a thermal mass / heat-sink. I don't mind it not being concrete (it can be contained water, rocks, adobe etc) but it has to be had. The lowest-hanging fruit is to passive-solarise the existing housing-stock - with an eye on Homestar Rating or something similar.
Lastly, wood is good - but why the ---- do these Green Growth types advocate techno-fixes for inferior material? Radiata is crap, and should be phased out. Macrocarpa is orders of magnitude better, Douglas fir, even some eucalypts, than something which needs soaked in poisons to poison the organisms which like to feast on it.
But those wooden houses will expect to be 'more', serviced by 'more'. More FF roading (bitumen), more FF pipework (plastics), more FF fuel (diggers etc). This on a planet with 6-7 billion too many people, in a country with 2-3 million too many people, and which is hemorrhaging chemically/physics-wise already. It's just self-justification by one species. We need to be not-building. There is enough accommodation already - if it was spread around equitably.
I disagree that fossil fuel supply is more of a restraint than climate change. For the world to survive into the next century fossil fuels need to remain in the ground.
Cities can go fossil free IMO - they can be electrified with renewable generation- this is certainly possible in NZ.
If urbanisation needs to be reversed then the greater part of humanity will not make it.
I discuss more of these points in the expanded version of the article.
Surely it must be easier to supply energy to a city rather than if the population was spread out.
No. Capturing energy as close to source as possible, is best/least loss.
But it's also the energy required to get the food/materials in, and the wastes out.
At the end of the day, there are too many of us, versus sunlit acreage. Whether we crowd ourselves into one space or not, that's the crucial ratio. We skewed it temporarily by adding historic acreage (sunlit acres which became coal, oil and gas) which temporarily supported more of us. Most of that more, is domiciled in cities. Cities, ex fossil energy, never got above 1 million inhabitants, and there was a lot of dieoff/replacement churn at that level. Tells us how vulnerable they are.
But to your comment; close sunlit acreage per house, is best.
Yeah we have been of the grid since 2015 solar does most of the work and fortunatly we have lithium batteries. without the diesel generator we would be stuffed when we have visitors or the weather is bad. But to supply a multitude it would be much easier to not only supply energy but food to a condensed population, think intensive farming.
'slow-growing, tropical hardwoods' - many tropical hardwoods are not slow growing and far out strip growth rates of radiata pine. NZ is in danger of pricing itself out of the market.
'Intensively managed plantations account for 1.5% of the world’s forests, but they meet one-third of the demand for wood products. Eucalyptus plantations are among the most productive, with rates of growth depending heavily on genetics, silviculture, and climate.'
Kiwirail currently replacing millions of sleepers with concrete ones. A played wood solution would be good.farm and road bridges could be also engineered wood.an old Dutch customer of mine showed me some vehicle blocks he had made, he simply routed a grove and glued a piece of plywood across the grain, strong as.
Now we just need NZS:3603 redone to make it an acceptable solution
We welcome your comments below. If you are not already registered, please register to comment.
Remember we welcome robust, respectful and insightful debate. We don't welcome abusive or defamatory comments and will de-register those repeatedly making such comments. Our current comment policy is here.