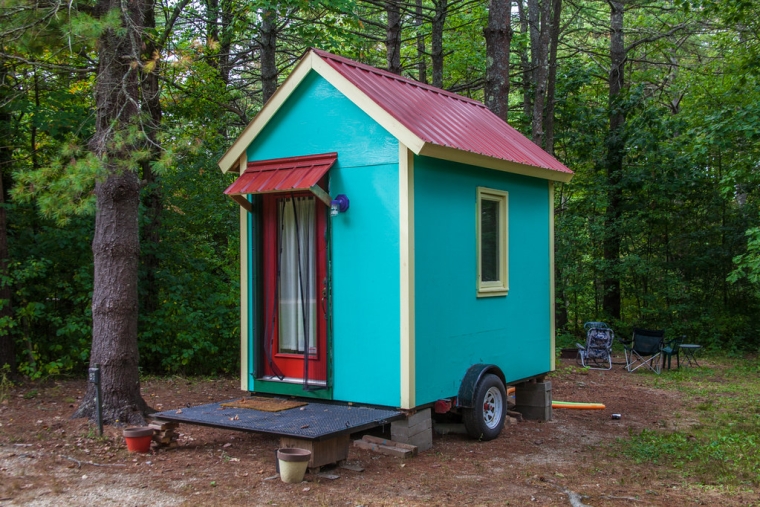
Residential construction costs are continuing to rise rapidly even though the average size of new homes is declining.
Statistics NZ figures show that 37,538 new dwelling consents were issued in 2019, up 13.8% compared to 2018. The biggest increases occurred in the Tasman Region +26.9%, followed by Gisborne +21.7%, Taranaki +20.9% and Auckland +17.8% (see Table 1 below).
Not surprisingly, the biggest increase in absolute numbers was in Auckland where the number of new dwelling consents rose from 12,862 in 2018 to 15,154 in 2019, accounting for 40.4% of all consents issued across the entire country.
The only regions to record a decline in new dwelling consents last year compared to 2018 were Northland -3.2% and Manawatu/Whanganui -2.2%.
While the number of new homes being consented has been increasing, their average size has been decreasing for almost a decade.
The average floor area of all new dwelling consents issued throughout the country has been in more or less steady decline since 2010 when it was 200 square metres, with the decline gathering pace since 2014.
Last year the average floor area of all consents issued was 158 square metres, down 21% compared to 2010 (see Table 2 below).
That decline is not just due to more high density properties such as apartments being built, because a closer look at the figures reveals that the average size is declining for almost all residential property types.
The average size of stand alone houses being consented has declined from 216 square metres to 2010 to 194 square metres in in 2019 (-10.2%), townhouses and home units have declined by 6% over the same period from an average 116 square metres to 109 square metres while average apartment sizes have declined by 13.8%, from 109 square metres in 2010 to 94 square metres last year.
The only type of residential dwelling not to record a drop in the average size since 2010 was retirement village units, which recorded a marginal increase of 2.6%, from 115 square metres to 118 square metres, although retirement village figures tend to be more volatile than those for other housing types.
Over the same period, average construction costs have been steadily rising.
In 2010, the average construction cost of all new dwellings consented was $1394 per square metre (excluding non-construction costs such the cost of land and marketing expenses), and by 2019 that had increased by 67.6% to $2337 per square metre.
That pushed the average construction cost per dwelling up by 32.7% over the same period, from $278,209 in 2010 to $369,318 last year.
The good news in the cost figures is that the greater proportion of higher density homes such as apartments and home units being built in Auckland does appear to be bringing down total costs per unit, even though costs per square metre continue to rise substantially.
Between 2010 and 2019 the average cost of new dwellings consented in Auckland shot up by 74.9%, from $1411 per square metre to $2468 per square metre.
However the rising costs of construction in Auckland have been mitigated by the growth of multi-unit developments in the city, which have pulled down the average size of new dwellings.
In 2010 multi-unit developments such as apartments, home units and townhouses accounted for just 9.6% of all new dwelling consents issued in Auckland, but by last year that had increased to 50.6%.
That brought the average size of new dwellings consented in Auckland down by 30% over the same period, from 219 square metres in 2010 to 153 square metres in 2019.
That drop in average dwelling size saw the average total construction costs of all new dwellings consented in Auckland peak at $399,453 in 2016 and it has since fallen back by 5.2% to $378,577 last year, even though costs per square metre are continuing to rise strongly.
The figures suggest marginal savings in construction costs in Auckland are being achieved by reducing the average size of the new homes being built.
The challenge for the building industry is make significant reductions in the per square metre costs of construction which could have a more meaningful impact on the cost of new housing and its affordability, particularly for first home buyers.
That will likely depend on the introduction of more efficient construction methods, possibly such as greater use of high volume, prefabricated construction techniques and making the supply chain more efficient and competitive to bring down the cost of building materials.
The comment stream on this story is now closed.
Table 1:
New Dwelling Consents Issued by Region 2018-2019 | |||
2018 | 2019 | % change 2018-2019 | |
Northland Region | 1,156 | 1,119 | -3.2% |
Auckland Region | 12,862 | 15,154 | 17.8% |
Waikato Region | 3,742 | 4,251 | 13.6% |
Bay of Plenty Region | 1,996 | 2,146 | 7.5% |
Gisborne Region | 83 | 101 | 21.7% |
Hawke's Bay Region | 621 | 714 | 15.0% |
Taranaki Region | 464 | 561 | 20.9% |
Manawatu-Whanganui Region | 1,201 | 1,175 | -2.2% |
Wellington Region | 2,731 | 3,174 | 16.2% |
West Coast Region | 126 | 139 | 10.3% |
Canterbury Region | 4,769 | 5,308 | 11.3% |
Otago Region | 2,001 | 2,286 | 14.2% |
Southland Region | 281 | 321 | 14.2% |
Tasman Region | 394 | 500 | 26.9% |
Nelson Region | 303 | 312 | 3.0% |
Marlborough Region | 258 | 276 | 7.0% |
New Zealand | 32,996 | 37,538 | 13.8% |
Source: Statistics NZ |
Table 2:
New Dwelling Consents Issued in 2019 | ||||
Average Size and Cost | ||||
Number issued | Average value per consent $ | Average floor area sqm | Average cost $/sqm | |
Northland Region | 1,119 | 414,006 | 184 | 2,250 |
Auckland Region | 15,154 | 378,577 | 153 | 2,468 |
Waikato Region | 4,251 | 352,204 | 163 | 2,160 |
Bay of Plenty Region | 2,146 | 379,917 | 162 | 2,338 |
Gisborne Region | 101 | 372,170 | 163 | 2,286 |
Hawke's Bay Region | 714 | 426,524 | 180 | 2,364 |
Taranaki Region | 561 | 363,095 | 183 | 1,988 |
Manawatu-Whanganui Region | 1,175 | 333,438 | 168 | 1,980 |
Wellington Region | 3,174 | 333,039 | 130 | 2,562 |
West Coast Region | 139 | 288,943 | 149 | 1,940 |
Canterbury Region | 5,308 | 345,746 | 164 | 2,114 |
Otago Region | 2,286 | 426,628 | 164 | 2,600 |
Southland Region | 321 | 355,412 | 180 | 1,973 |
Tasman Region | 500 | 359,611 | 167 | 2,154 |
Nelson Region | 312 | 332,656 | 138 | 2,407 |
New Zealand | 37,538 | 369,318 | 158 | 2,337 |
69 Comments
Where do these numbers come from? $1394/m2 in 2010? Really? Could you really build a 100m2 3 bed home for $139k?
Yes. More importantly, assuming this data is correct, the whole idea of economies of scale seems to be back to front in NZ. For a basic need, this is not sustainable without bucketloads of money printing and / or higher h'hold incomes.
Yes you could, but don't forget you need to add GST, finishing materials (carpets, drapes, appliances such as fridge/freezer), landscaping, possibly the driveway and of course the price of the land. Finally these numbers come from building consent applications and most builds end up about 20% over so… there you go
Finally these numbers come from building consent applications and most builds end up about 20% over so
Right. So that suggests that too many are feeding off the housing industry thereby pushing costs up. Ultimately the consumer loses.
How do you come to that conclusion?
Simple. Market distortions caused by cost-inefficient regulation.
Too much theoretical fluff J.C. it's much simpler than that, cost overrun by 20% because of the clients variations during construction. (at the time of applying for the building consent any decent Architect would have a tender with a fixed price, I know, I had my own Architectural business for 18 years)
You just kind of illustrated my point
No, not in the slightest bit, you blame it on "regulation" (check your previous post) I tell you very clearly it is because of the changes the owners make to the house after the building consent has been issued
I see. It's all the "consumer's fault."
Yes in this case it is, I have designed and project managed many, many buildings, we start with detailed plans and specifications and a locked, fixed price contract to build. The cost overrun can only come from changes to the plans or specifications and these are always done by the clients. I'm not blaming them at all, it's kind of normal to want to change some things as construction progresses.
Well, anecodotally... my wife is a builder (nearly finished apprenticeship) working on both new builds and renos. It does seem like *every* client decides at some point that actually, they'd prefer the window over there... and a wall in there... you can tell them that they now need to buy $40,000 of materials and add a month to the construction time, but they've spent so much money already by that point, it's like confetti to them.
Indeed
I think you'l find permit build costs are priced conservatively, to reduce the cost of permits.
Local governments rarely; if ever, audit build costs. Easy to do with group home companies, but Council are too scared to touch them.
Dont disagree with variations from the original build, which can change the cost per square metre considerably.
Indeed
Could you really build a 100m2 house? regardless of price. Most subdivisions I have seen recently have minimum dwelling size of 120m2, one was even 150m2.
Many subdivisions have covenants imposed by the developer requiring minimum sized houses.
That is ridiculous, like an AR15, people don't need a 120m2 house and owning a large house is an act of violence against people who can't afford it.
This comment makes no sense. Why would owning a big house have any impact on those who cannot afford one? Or for that matter owning any house. Your comment can be translated to saying owning a home is an ct of violence on the homeless. Just plain idiocy and extremist jealousy!
Section we were looking at had min 200m2, amongst other things.
200k will get 185sq 4 bed 2 bath in Aussie with air/heat pumps in every room, solid block construction etc.
200k will get 185sq 4 bed 2 bath in Aussie with air/heat pumps in every room, solid block construction etc.
Yes the cost per m2 has gone up considerably over the last decade but so have the specifications, better foundations, ventilated facades, double glazing, better insulation, HVAC, smarter lighting solutions and appliances, better plumbing fittings etc… Construction costs are not about to come down
That demonstrates market inefficiency more than anything else. The automotive industry is a good example of where consumers can purchase cars based on their needs and budgets. If manufacturers cannot produce construction mats that meet consumer demand, then ultimately their businesses fail.
Not comparable, cars are produced en "masse", making 100's of thousands of the same (+/- some options), most houses are designed and built individually and they have to be in response to the site, e.g. N/E/S/W facing, topography, access, views, owner desires and preferences etc...
Actually, Japanese car buyers can choose what they want and need directly from the manufacturer. Similar with housing through the likes of Sekisui. Very comparable.
No, you cannot produce 100'000 houses in a factory and then somehow transport them all finished onto vastly different sites. J.C. stick commenting on issues you know
Sekisui is an ex-client of mine. Know their business very well.
I'm sure you do but it doesn't change that you cannot produce 100's of thousands of finished houses in factories and somehow ship them to very different sites.
Prefabrication shouldn't just be thought of as shipping finished houses out of factories. Decent gains can be accrued with prefabricating house components.
So so wrong. That is exactly what is coming from one of NZ's wealthiest families:
https://www.nzherald.co.nz/business/news/article.cfm?c_id=3&objectid=12…
Vastly increased up-front costs for relatively tiny improved utility. Reality is that additional regulatory burden has eaten up a great deal of that extra cost. Money down a hole on supporting a whole lot of shiny bums in offices. It is not showing up in bricks and mortar.
Yeah, those shiny bums have no idea we were happy with our wet cold leaky buildings. Bit of mold in the walls? No worries, at least the developer 10 years ago saved a few dollars on the consent fees.
The developer just puts the cost on the end user?
Leaky houses mostly came from architects going to flat roofs, no eaves, untreated framing and unconventional cladding. The regulatory response has been monstrously uneconomic. NZ was screwed over by inefficient remediation process where lawyers ate up 5-10x more than fixes. Heaping hugely higher costs on new-builds with regulatory compliance costs and armies of risk averse building professionals over specifying everything to a crazy degree to prevent even minor failures is a ridiculously expensive 'fix'. Far better to remove council liability and budget an average of few hundred dollars a year (insure if you want to) in house maintenance over long term.
Leaky houses came from a time when Yvil was still an architect......
Low blow, I take offence to that comment
All these failed experiments came branz approved. If we could rid ourselves of branz and the fletchers/carters/ hardies cartel it would be a step in the right direction.
Let's count some of the increased non-build overheads:
- Scaff everywhere - typical costs $2000/wk
- Fencing of site typical costs $500/week
- Certification of every power tool, extension cord, supply box etc quarterly - typical cost $20-50/tool/inspection
- Elfin Safety meetings to discuss site hazards, maintain register of all visitors, tradies, inspectors, local sparrows. Typical time 1-2 hours per day shared over all warm bodies
- Certification of all tradies including the 'how not to fall off a ladder' credentialism which has crept right through the sector - the increase is in time lost to keeping papers current, and to time lost to the 'education' effort needed in the first place
None of these existed at all 20 years ago.......typical cost component of a new house is 10-15% for fairly much zero benefit in practical outcomes. /rant
Not wrong there.. we're not in construction, but working on industrial sites, and many of these costs apply to us. It seems we've just seen the last of the sparky testing and tagging all our leads and tools and 4 weeks later he's back to work his way through the lot again. Wasted a day last week on the First aid refresher. Forklift one must be due soon too.
The various site inductions (One for each site, then one for each department on that site you need to work in) and revising/updating Safe Work Method Statements and the like typically chew up another working day a month.
Construction costs are not about to come down
They are not, as long as the RBNZ persists in it's pursuit of cutting interest rates in half - three times since Jul 2008.
What's your logic for linking construction costs and interest rates?
When the Fed engineered its experiment to promote the wealth effect, the family with savings experienced an increase in the present value of their assets and also an increase in the present value of their liabilities. Because our financial assets are traded in markets and because we receive mutual fund and retirement account statements, we promptly saw the change in the value of our assets. We are much slower to appreciate the change in the present value of our liabilities, particularly the value of our future consumption expenditures.
But just because we don’t trade our future consumption expenditures on the stock exchange does not mean that the conventions of finance do not apply. The family with savings likely ends up where they started, once we consider the necessity of revaluing their liabilities. They may more readily perceive a wealth effect but, ultimately, there is only a wealth illusion. Link
More theoretical fluff. I asked you how you link the RBNZ and construction costs, then you post someone else's view on the Fed and asset values. The Fed is not the RBNZ and asset values are not construction costs. Why don't you answer my question in your own words? (btw, there's no need for the blue background either)
Unless there is a technological improvement, construction costs will not come down as there is a minimum wage floor under them and that goes only one way: up. You cannot reduce the costs. Sure if interest rate were higher, less people could have borrowed. This would have reduced profit margins for a short time (more competition for a smaller market) and would have affected land price to an extent. But the replacement cost (i.e. adding the same infrastructure on a new land as the one currently in place in a comparable location) would have limited the drop in land value and commercial viability would have reduced the drop in profit margins.
I am not sure what the impact of dropping demand would have had on construction material, as that market seems to be a monopoly or duopoly.
Overall, interest rates affect ability to consume not that much ability to produce. If no cheap money, then construction sector will go bust, without construction getting any cheaper. Labour, fuel, etc too expensive and not affected by interest rate.
Theoretically, at least, mass prefabrication could reduce costs or at least stem their increase.
Yes when the cost of financing is reduced it acts as a disincentive for developers to innovate as well as sharpening the price. Development 101.
Most of those changes were more than a decade ago, try 2007 for Double Glazing and Insulation. That is not the reason for the cost increases in the last decade.
For the sake of the customer the building supplies industry desperately needs a productive and competitive new entrant.
You're talking about radical changes in the business model. Not easy in a country like NZ with a small population and relatively far proximity to suppliers. Can be acheived in Europe, U.S., Asia, and Japan. Maybe not NZ. Size of prize not big enough.
Yes there's market failure. Our small size is a big factor in that.
Who plugs the gap when there is market failure?
How about the government...???
Labour needs to stop being Tories in drag
What part of this is surprising though? very expensive labour force (a fact) that is not very effective (not a fact, just personal experience). The expensive labour has a huge impact as it is a compounding factor that affects many components (direct labour, materials and handling of the material, all professional services, regulatory and supervisory activities, infrastructure costs included in the land value etc). Expensive health and safety, expensive construction material, 15% GST, expensive equipment, expensive fuel, etc.
Yes. And if the labour component became more efficient and productive, they would be cutting their own throats. No incentive to offer more for less.
Did anyone mention the fact that not only the houses are getting smaller, so are sections to put them on, all in the effort to get the cost down so something the masses can afford to buy. Plenty of places in Tauranga, Papamoa I looked at you cannot swing a cat on now. Sections down to 360sq/m and so close to the boundary you can shake your neighbors hand if you both lean out the windows. With all the land in New Zealand its really turned into a pathetic situation to be in. Even if you HAVE the money you don't want to spend it on some of what they are now calling a house.
I saw one for sale at 250m^2. Hard to believe you can fit a house on that, but they seemed to have plans which must have run right to the allowed boundaries. And at a mere million bucks, what a deal.
With thoughtful design and build you can have a wonderful house on 360sq/m. In many cities that's actually a pretty big block.
But it needn't be that way in a country the size of ours with less than 5 million people.
Average cost per m2 leaves a lot to be desired as a way of measuring build cost. Having looked into it a little (in the absence of much in the way of new listings, thinking about building), I get the impression that you'd be hard pressed to stay under $3000/m2 in auckland at this point, unless you somehow have a dead flat section and you're quite economical in your build.
In any event, I'd expect the cost per m^2 to rise as the consented size falls. There's only one kitchen, regardless of being a 120 m2 townhouse or a 350 m2 monster. Amongst other things, that means that the rates /m2 tend to be lower in larger houses.
Exactly
There is considerable focus on construction costs, when, quite possibly, there are other significantly growing costs in some areas. GST on new build sales and RE costs = 16%, Finance and the compliance requirements (QS etc) 3.3%, Services and fees (for council) 4.5%, Consultants to achieve RC and BC = 4.5%, land and prelim works = 4.5%, construction including foundations = 40%, and of course the land component at around 10-15%, and finally admin costs. These are approximations and based on a more intense development. The smaller items certainly add up and the process inefficiencies are quite surprising.
Costs will keep rising as in all other sectors because there is no pressure on the monetary supply from which to borrow, until there is pressure at which point price growth will slowdown...
The big problem in my sector is that every aspect of the chain of supply is affected by complete lack of scale which makes supply chain horribly expensive. Also has anyone even seen how much material goes into a foundation these days? With sesimic type requirements going up all across the country there is a huge amount of groundwork to go in long before you cost out carpets and blinds. The days of a simple ring foundation atop a compacted heap of rubble are long gone, not that that was an adequate solution anyhow...
But the old foundations worked fine by and large. Adding 5-10% cost to every house to save a possible once in 100 year event that wrecks a few percent of houses due to weaker foundations is terrible economics. I've lived in a couple of 80 year old villas that were still on their original shallow wooden piles in concrete. Those houses are still doing fine, might need a few 1000 in additional pile maintenance every few decades.
So, 50% of what is consented in Auckland is now not a decent house with a garden, which is what people with kids want and need. And this is to be seen as an improvement?
People are offered 10% floor less for about 75% more price than 10 years ago.
What an achievement.
No wonder sales in 2019 were lower than in 2009, despite 13% increase in stock, a pop increase of about 250,000 and interest rate costs reducing considerably.
Of course, it is still "affordable"
So from article numbers looks like regulations have added costs of ~$700/m² in real terms in last 10 years, which for average 200m² house is $140k and for 30k houses a year is $4billion dollars of wasted money. How much is all that extra regulation saving in ACC and house fixes. bet it is not even a tenth of that. If you want affordable houses then wind back the relevant regs and regimes 10-20 years. GOVT please fix this!!!
In ChCh you can build a 200m2 house for around $650k in a reasonable subdivision and on approx 600m2.
Some less and some a bit more depending on site and quality and fittings.
250k section and 400k for house plus furnishings.
Yes there are many pathetic 300m2 sections that have small homes on them as well which is clearly catering to a market.
Many of the good subdivisions in ChCh you wouldn’t be able to build something so small as covenants prohibit this.
Families in general in the future are possibly going to decrease compared to 30 years ago as well so homes not needing to be as large.
20 years ago we built a home of over 500m2 and cost approx $250k or $500 per square metre that same house today to build would be in excess of $1 million however it would be unbeleivably better than the cold weatherboard box’s in Auckland
We welcome your comments below. If you are not already registered, please register to comment.
Remember we welcome robust, respectful and insightful debate. We don't welcome abusive or defamatory comments and will de-register those repeatedly making such comments. Our current comment policy is here.