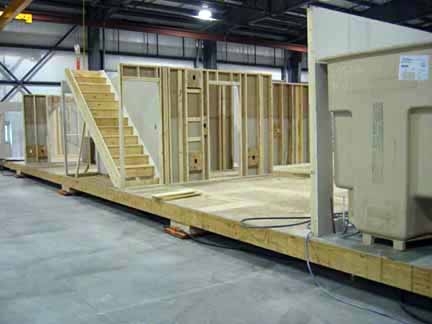
Large scale prefabricated housing construction has come a step closer with the Government's KiwiBuild scheme issuing an Invitation to Participate (ITP) to building companies capable of developing suitable offsite manufacturing operations.
The ITP invites suppliers to present proposals for delivering modular homes that meet KiwiBuild's criteria for design, manufacturing and assembly.
When the Government announced its plans to build 100,000 affordable KiwiBuild homes over the next 10 years, it said prefabricated construction may be one way of bring down the construction cost of dwellings.
The Head of the KiwiBuild programme, Stephen Barclay, said exploring the opportunities that offsite manufacturing could offer in terms of innovation and scale could drive a real step change in the availability, quality and cost of affordable housing.
"While the first KiwiBuild homes in Auckland are already on the market and we have deals with a number of developers around the country for hundreds more over the next 12 months alone, offsite manufacturing has long been identified as a potential game changer," Barclay said.
"When we look at the proposals, consistent quality will be a high priority alongside other inherent benefits off-site manufacturing should offer, such as reduced construction costs and speed to market."
Interested companies have until November 12 to respond to the ITP and shortlisted respondents will then be invited to make their case to KiwiBuild's evaluation panel in the first quarter of next year.
Individual contracts will then be negotiated with the individual companies that are selected by the panel, so it could be well into next year before negotiations with interested building companies are finalised.
You can receive all of our property articles automatically by subscribing to our free email Property Newsletter. This will deliver all of our property-related articles, including auction results and interest rate updates, directly to your in-box 3-5 times a week. We don't share your details with third parties and you can unsubscribe at any time. To subscribe just click on this link, scroll down to "Property email newsletter" and enter your email address.
40 Comments
Perfecto. . Will help existing house prices to fall. . Build in scale, efficiency and productively
Should start talking to the big pre-fab operator in the Hutt who recently folded.
This time it's going to be different - as they say.
Well I must give credit to the government for really pushing on with Kiwibuild. I admit being dubious on the 100'000 affordable homes in the next 9 years but at least they are persisting and trying their best.
Yvil, isn't it so refreshing to finally have a Government that's trying its best? Many years of little change as given birth to a many like minded gloomsters! Having a little faith will get you a long way :-)
Agree. The previous government had misplaced over confidence in the market. This is a great move, gives prefab businesses the certainty of work regardless of market volatility.
We are looking at building a simple 2 bed <80sqm next year and are looking at different options such as pre-fab, which I am quite keen on. But they are not less expensive than a kitset or conventional build as far as we can tell. If there are any efficiencies gained they are being pocketed by the companies themselves. Overall the cost of building is ridiculous and it is easy to see why there is a constant shortfall.
Kiwibuild will hopefully help give some scale to these prefab companies but it is obvious that as long as our building costs and consent/council costs remain at these levels then building rate will fall short.
Has anyone seriously compared the cost of pre-fab vs building in NZ, I'd love to see a cost comparison.
From what I understand, direct costs are essentially the same, the cost benefit is in the time savings. Your pre-fab won't be held up by weather, the site prep is done parallel to the house build and you won't be delayed by subbies. What that means for the home owner i'm not sure (less time & stress I imagine), the developer it's the cost of time where they benefit. The intangible value is the quality, factory builds are better quality allegedly.
In saying this, if you ordered 300, I'd say the direct costs would be lower.
I dont understand, why would direct costs be the same if you are cutting labour time so significantly? Sure, materials would remain similar but they must be able to pass on savings from decreased manufacture times.
Delving into my texts, the labour cost savings for mass production are expected to follow this pattern
1 unit 100%
2 units 90%
8 - 73%
32 - 59%
128 - 48%
1000 - 32%
This is a fairly modest learning rate and the savings could be twice this.
The cost of materials could be similarly expected to drop. Wasn't it Lenin or Marx who said something like the cost of all products represents the labour cost embodied in them.
What's the bet that once again Fletchers are the big winners with this.
If they go down the prefab route, they should also look at building above code. When you are factory building panels, it is not much effort or extra cost to increase stud size, add more insulation and an airtightness layer. You can even put insulating windows inline with the insulation so they perform as they should.
I have spent a lot of time staring out the window considering this whole energy efficiency thing may be just a rort.
If the house is energy self sufficient which may be feasible in another decade why would we spend unnecessarily on insulation or energy recovery systems.
In other words a solar panel roof tile construction may relax the requirements for insulation and ventilation allowing a cheaper and healthier house.
You think?
You should stare at the windows to see the problem rather than out of it. Cold, wet, mouldy frames and the resulting poor health outcomes don't get fixed by solar panels, neither does interstitial condensation, air quality, thermal bridging and drafts.
It is much easier to be energy neutral when you energy needs are reduced. I currently generate 1.5x the energy I use but as this is mostly generated when I am not home, I struggle to use it so end up buying electricity at night time. You could heat the house during the day when the sun is out but unless you have improved the thermal envelope then you won't be able to maintain the warmth until the sun is up the next day.
Battery technology won't save you here as you would need to halve in price to break even. It is unlikely ever to be cheaper than a distributed grid system in a populous area due to economies of scale.
Was watching some videos of this crowd on YouTube the other day: http://www.nzsip.co.nz/introduction/
Looks very interesting and positive to me. Someone who knows more than me may be able to chime in with what's not great about the approach.
SIPs are a good solution. They need a bit more detailing around the openings and roof/midfloor joins. They are inherently airtight so a ventilation system is needed to prevent condensation and pollutants getting trapped inside.
William Levitt showed how it could be done in the 1950's. Those assembly line style construction methods on a large scale site combined with onsite warehouse yard to receive direct from overseas suppliers containerised shipments of everything that goes into making a house would cut the costs considerably. Prefabricate as much as possible offshore and design every component so it can stow in a 40' high cube container. All-terrain forklift and mobile crane truck permanently on site to make continuous deliveries of the required components to sites as required.
No BRANZ approvals in those days !
Importation is very difficult once you add on transport - no USA as still imperial, no non standard Gib board lengths etc ex our domestic cut to length operation.
Bulky items such as roof trusses will always be local - no import option there.
No insurance without approvals.
In descending order of finished total cost - none substitutable with imports.
Land
GST
Utility connections
Council approvals
Labour
Materials are WAY down the list so until you address the above - there will be no significant savings in Kiwibuild costs.
But if the KB hooses, from wherever, are plonked into a UDA development area, then all the consenting palaver is neatly sidestepped. Part of the point of a UDA is shurely that it is it's own BCA, thus dodging the Council wallahs, BRANZ, and all the other handbrakes. At least one Hopes that that's the intention, and that it does not just substitute one set of cost-and-time-adding Brown Cardies for another....
Glass Half Full, the UDA promoters have perhaps been reading this site, and wising up....
Have to wonder if the COL will subsidise KB homes by putting the cost of normal council fees on other builders and rate payers?
Land - Brown Field sites where government entity already owns the land
GST - Money out money in for the government
Utility connections - Can be negotiated down on a large scale
Council approvals - Can be legislated away. Governments make the law.
Labour - You don't need someone that can build an entire house. You just need someone that can assemble one small part (under supervision) of 100's or even 1000's of houses. A workforce structured in that way can achieve more than an army of bespoke builders.
The supply chain costs and markups applied at each touch point from manufacturer/importer through to the actual building site are not to be underestimated.
Someone gave me some great links on here a while back re the effect of growing regulation on house building, and the issues this helped cause when leaky homes were built.
Would be great to see much of this regulation backed out for a more simple model (a la Tokyo) and greater requirements around warranties and an industry fund/ insurance for managing quality issue costs over time.
BRANZ and all the associated cartel bullsh8( that drives it is a rort. The whole system needs tearing down.
Yes,
We should go back to the time when councils supervised connection of water systems and that was enough.
House design should be the responsibility of the builder and any materials can be used as long as they are certified to some nations standards.
It wont happen.
@ kiwiemn
I agree with your comments. Can you tell me what are insulating windows? Are they double glazed windows?
Insulating windows do what they say - they insulate you to prevent heat loss. This means the glass and the frames should be insulated - non-metal frames (even the thermally broken aluminium windows are useless) and Low E double glazing as a minimum. Aluminium is used for saucepans as it is the best common metal for conducting heat.
They need to be mounted in the middle of the wall so that the inner surface is in the warm part to make them work as an insulating layer, Current practice is to mount them as part of the cladding which allows the cold to flow around the back of the window via thermal bridging. See an explanation here https://www.eboss.co.nz/detailed/jon-davies/improve-thermal-performance…
The rest of the western building world laughs at our approach to windows.
I recently had some windows and doors priced. White uPVC frames were a $17k upgrade beyond standard alu. Coloured uPVC another $27k! Thermal break $9k more.
I wasn't confident the thermal breaks would be installed to perform correctly. I also wasn't confident the uPVC windows would seal well as I had seen complaints on forums where the NZ companies had put hinges over the rubber seals.
I went with the standard alu frames + lowE. If I had gone uPVC I'd be paying $750 more in interest and I'd rather use that for heating. The foundation was a similar story; $13k to insulate the slab. I ended up just going to with thicker framing as it's cheap but probably doesn't make much sense.
After all the costs from councils, BRANZ, health and safety, ripoff subbies etc there isn't much room for proper insulation.
Yawn!!
Translation "I totally misjudged the Coalition and it hurts like hell being proved wrong"
RP! They have nothing of any benefit at all since they have been in power!!
They are falling apart at the seams, if they actually had seams.
Prefabs were mentioned months ago and absolutely nothing.
Another working group required!
The KiwiBore homes that are supposedly finished at McLennan the developer doesn’t even know whether he is making money on them?
So the coalition govt is somehow responsible for the poor business practices of a developer? (if your statement is true.. which I doubt)
You have now reached Whine level 10.
Level 11 is next - Spinal Tap Level.
- ...why don't you just make ten louder and make ten be the top number and make that a little louder?
- These National whining devices go up to 11
Yes the new government is certainly getting things done in the housing area. As house prices continue to drop in Auckland and Christchurch it will get better and better for first home buyers. My wife's best friend is a property investor and even she said recently that her step daughter who is currently looking for her first home in Auckland should wait and let the market come back to her.
Gordon, comment on stuff you know about.
ChCh prices have not dropped whatsoever.
Is there actually even a housing shortage ? or is it an integrity shortage ? How many foreign asians own properties here that are vacant ??? How many Baby Boomer property scalpers are there robbing the younger generation of there own home and forcing people to become rental slaves ??? My 94 year old grandmother claims her husband and herself where only allowed to build one house for themselves and own a maximum of one rental property to stop what we are seeing happening today. Does anyone out there have any record of this happening ?
Pretty hilarious when you realize that these prefab houses will be of better quality than the existing stock.
Why do I get the feeling this will go to Fletchers or Carters with the justification being they have 'local experience' or some such lies.
If there is any involvement with those rogues from Fletchers we are all &^&%$ed
We welcome your comments below. If you are not already registered, please register to comment.
Remember we welcome robust, respectful and insightful debate. We don't welcome abusive or defamatory comments and will de-register those repeatedly making such comments. Our current comment policy is here.