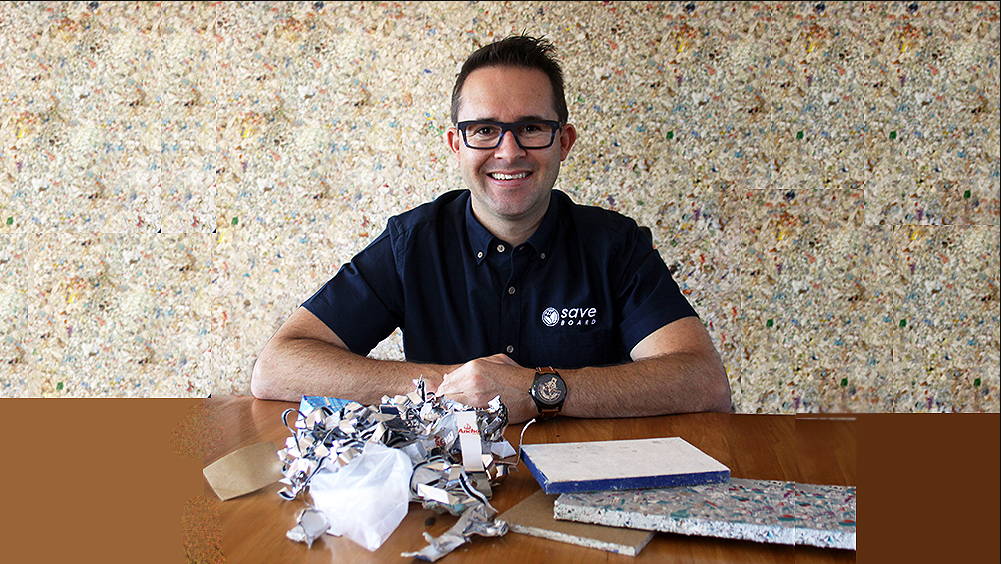
In June Prime Minister Jacinda Ardern said she was concerned about the supply of residential building supplies in NZ, and in particular, of plasterboard. Since then we've seen the introduction of a Plasterboard Taskforce and Winston Wallboard's stranglehold over the use of plasterboard for structural bracing was broken. But what difference has it made?
The maker
One new plant each year.
SaveBOARD co-founder Paul Charteris’ business has been up and running for nine months, with its one New Zealand factory cranking out 500 boards each day made from chucked out coffee cups and rubbish, and plans to open its first Australian plant in three months time — backed by a more than A$1.7 million local and central government grant.
The environmentally-ambitious firm has big business plans and the global interest to match; Charteris says he has fielded calls from Israel and Asia, he recently sent a container of product to interested parties in Chile, and expects its Aussie plant will swiftly be joined by others, with an ultimate goal for the startup of one new plant every year.
The firm produces a plasterboard product Charteris hopes can become part of a solution for both New Zealand’s reliance on GIB-branded plasterboard, and for the tonnes of waste heading into landfills.
Old coffee cups, milk cartons and commercial waste are turned into a range of plasterboard products at SaveBOARD’s Te Rapa factory which was officially opened in June this year, at the same time as the construction industry was grappling with a shortage of the essential building material.
But making inroads into New Zealand’s notoriously tight plasterboard market isn’t easy, even with the might of Building and Construction Minister Megan Woods and the Ministry of Building, Innovation and Employment (MBIE) urging on the use of non-GIB products like SaveBOARD.
In July Woods announced the first actions of the Plasterboard Taskforce, which included four alternative plasterboard products including SaveBOARD getting the tick to be used in New Zealand to satisfy Building Code requirements for structural bracing.
Charteris says the positive out of the plasterboard shortage is an openness to new or substitute products like his.
It hasn’t seen the order “floodgates open”, but it has helped the business, he says.
“Our products are quite similar, but different. They are direct substitution, but they perform or look or feel different. Probably a few years ago there would be higher resistance, whereas now people might say, ‘maybe it isn’t as perfect as what I used to use, but it has all these other attributes around sustainability, and the circular economy, but it doesn’t have the aesthetic finish of a traditional product’.”
The biggest barrier for the products is the process of making a substitution at all, Charteris says.
If a designer or specifier has picked a branded product, like the 95% market-dominating GIB plasterboard, he says it can be costly to change.
While MBIE has published guidance on which products can be used as a substitute to make it easier to work out what can be used instead of GIB, any substitution needs to be lodged with the building consent authority and then approved by an inspector.
That all has a cost, Charteris says.
“For a substitution that is a barrier. There is a cost to homeowners.”
The consenter
Auckland Council’s inspection manager Jeff Farensohn says a substitution using plasterboard on the new MBIE guidance might only take one of his inspectors 10 minutes to deal with and therefore not incur any additional costs.
But anything that takes longer would be charged at the council’s hourly inspection rate, which starts at $174 per hour.
He says at the “substitution” peak the council was getting roughly 40-to-50 minor variation requests each day.
Farensohn says that is about a 30% increase on pre-Covid times, and estimates about 20% of builders might choose a substitute product.
But more recently, it’s back to business as usual.
Farensohn says wait times for plasterboard have reduced, as has the interest in substitutes. While substitute products already ordered and delivered are being installed, plasterboard orders were now matching delivery timeframes, he says.
He’s not picking a plasterboard glut, yet, but substitute products already ordered should help to keep a lid on potential supply crunches.
As for issues with the new GIB-wannabes on the block, Farensohn says he’s yet to see anything proven.
“Social media has a lot of photos being posted of dodgy looking plasterboard. I've seen photos where the plaster was falling out when they cut the sheet between the paper layers. I had another photo given to me yesterday showing the bubbles in the plasterboard sheet. It didn't look normal. I wouldn't share them because you do occasionally hit people putting stuff online, probably from another country or whatever. I have principal specialists that actually follow those things up and we try to trace back to where it originates. And I haven't had any substantiated yet.”
He says he understands there can be a “natural hesitancy” for consenting authorities if they’re tossing up whether or not to allow a substitute. Cladding has to perform for 15 years, while structural components need to perform for 50.
Consenting authorities have to “look a little bit deeper”.
For example, imported products may come with international standards that can be mapped across to New Zealand standards. But that takes scope and expertise.
Auckland Council, as the largest consenting authority, has the in-house ability to work out how those international standards can line up with NZ standards, and can investigate and trace new products and their testing, Farensohn says.
That’s a big ask for smaller consenting authorities with more limited resources, but Auckland is sharing its knowledge where it can.
“Unfortunately, we do still find product that doesn't meet the mark. And that’s the sort of thing that keeps people in that risk-averse mindset, because they know that they're out there.”
It is not just plasterboard swaps that building consenting authorities like Auckland Council handle.
Farensohn says the most common requests for consenting variations are changes in layout, or moving a window.
Before plasterboard shortages hit the news, Farensohn says particle board or plywood for flooring was in short supply and therefore substitutions rose.
Cladding substitutions, along with plasterboard, round out the council’s top four most requested variations, he says.
The minister
Plasterboard has certainly got minister Woods' attention. She has set up the aforementioned Plasterboard Taskforce and finally got movement on the issue, after a shortage quickly turned into a crisis, from MBIE which released detailed guides for consenting authorities on how to chose, and use, plasterboard substitutes.
Woods told Interest in an emailed statement that more and more plasterboard is arriving into New Zealand on a weekly basis.
In July nearly 531,000 square metres of plasterboard and plaster-related products valued at $2.5 million were imported into New Zealand.
And in the week ending August 21, nearly 112,000 sqm worth of plasterboard and plaster-related products with a $506,000 value for duty were imported.
Woods said she had also written to all building consent authorities to encourage the use of MBIE’s substitution guidance.
In addition, the government house builder Kāinga Ora will be using alternative imported plasterboard in its retrofit programme, which will take some pressure off domestic supply.
“The increasing importation and use of alternative plasterboards is having a positive impact by alleviating pressure on the plasterboard market and providing market certainty for alternative products.”
4 Comments
"Woods said she had also written to all building consent authorities to encourage the use of MBIE’s substitution guidance." Hopefully Akl don't ignore that list as its a money spinner at $174/h for them to drag out any change on plasterboard for bracing. No problem with importer Joe Soap who knows nothing about building standards and specifications being blocked but why does Akl charge the architect or builder who passes on the cost to the home owner? It's the importer who should be charged. Wouldn't also be surprised if Akl pass this cost on multiple times.
The consents department is no doubt a money spinner for Akl hence the profit Akl made in the last year.
Good article.
It amazes me that houses built hundreds of years ago, without any certification, still perform. How could that be? And not one of them will be constructed of something the consistency of chalk, covered in paper.
https://www.youtube.com/watch?v=n-sQSp5jbSQ
More seriously, this applies:
https://www.goodreads.com/book/show/477.Collapse_of_Complex_Societies
And there goes $174/hr compliance.....
Back then the design was function over form.
Eaves to keep moisture away from the house.
Substrates and pitches to divert water.
Airflow to mitigate moisture buildup.
Then we wanted hermetically sealed cubes, or houses like the Mediterranean, which aren't subjected to the same volume of rain. Silicon as a moisture barrier.
The compliance industry in NZ costs a fortune for questionable gain. Buyer (or builder beware) would be preferable, if not for insurance issues.
'Stranglehold broken' ? , Construction of a new plant capable of 1.5x output of the current plant will be finished likely by this time next year (Tauriko) , this will significantly lift output . Now is the time for the 'pretenders' to take their shot at capturing some of the market but looking at the recent import decline tells me that window of opportunity may have shut itself quite securely, if the retreating RE market is considered. It is never going to be an 'easy win' competing with a well established and accepted brand. If nothing else is available of course folk will look at the next cab in the line but I think there are pluses with the locally produced product and as nice as it is to conveniently import product , it reduces employment and other opportunities for NZers. I dont think the stranglehold will ever be broken and yes it is nice to have a local product presenting itself as made from recycled wotnots , but I feel such would have limited appeal (niche value) coupled with an underlying risk factor that the time tested product nullifies. . Theres a very good reason folk favor the existing and its likely because they know and trust it , so much so that in times of scarcity they will pay above the norm to secure supply. The stranglehold remains for now and it will take a near miracle to break it.
We welcome your comments below. If you are not already registered, please register to comment.
Remember we welcome robust, respectful and insightful debate. We don't welcome abusive or defamatory comments and will de-register those repeatedly making such comments. Our current comment policy is here.